Introducción
En las acerías, los refractarios de magnesia-carbono (MgO-C) se utilizan como recubrimiento interno en diversos contenedores de acero líquido, tales como: hornos de oxígeno básico (BOF), hornos de arco eléctrico (EAF), hornos cuchara (LF) y convertidores LD (C. Atzenhofer et al, 2021). Estos materiales están, generalmente, sometidos a temperaturas superiores a los 1600°C (E. Benavidez et al, 2014) (Z. Liu et al, 2018). Además de los diferentes tipos de degradación termomecánica, estos ladrillos cuando están en contacto con la escoria (línea de escoria) deben soportar una fuerte degradación termoquímica (corrosión), provocada por el ataque de la escoria y la atmósfera circundante.
Las composiciones típicas de ladrillos de MgO-C contienen entre 80 y 93% en peso de MgO, entre 7 y 20% en peso de grafito y entre 2 y 3% en peso de antioxidantes (C. Baudín et al, 1999). Los agregados de magnesia electrofundida están formados por granos cristalinos, cuya unión se forma en el proceso de electrofusión de la materia prima. Por su parte, el grafito reduce el ataque químico por su baja mojabilidad con la escoria y el acero líquidos y aumenta la resistencia al choque térmico del ladrillo debido a su baja expansión térmica y alta conductividad térmica (C. Atzenhofer, 2021) (Z. Liu et al, 2018) (Y. Cheng et al, 2021) (E. Benavidez et al, 2015). Una de las desventajas de estos materiales es la alta susceptibilidad a la oxidación del grafito, formando una capa porosa descarburada en la que la escoria fundida penetra a través de los poros formando una capa de transición. Luego, los granos de MgO son erosionados por la escoria penetrada y se desprenden del ladrillo, lo que daña la estructura de los refractarios (J. Poirier et al, 2007) (B. Han et al, 2015) (Y. Liu et al, 2020). Para inhibir la oxidación del carbono, se añaden antioxidantes como: Al, Si o B4C, que reaccionan con el oxígeno retardando la difusión dentro del ladrillo (B. Han et al, 2015) (S. Zhang et al, 2001) (T.B. Zhu et al, 2016).
Las escorias siderúrgicas contienen diversidad de óxidos, principalmente CaO, Al2O3, SiO2, FeO/Fe2O3 y MgO. Los porcentajes de estos óxidos varían según el proceso siderúrgico en el que se utilice la escoria (E. Benavidez et al, 2015). Además de su composición química, se debe considerar el grado de saturación de MgO, el potencial de oxígeno y la mojabilidad entre la escoria y el refractario.
En el presente trabajo se discuten los mecanismos de corrosión basados en la microestructura desarrollada después de un ensayo de corrosión estática (cup test) a 1600°C de tres ladrillos de MgO-C. Estos ladrillos fueron diseñados para diferir únicamente en la calidad de la magnesia electrofundida. En el ensayo de corrosión se utilizó una escoria de convertidor LD. Este recipiente es de gran importancia, pues allí se desarrolla el proceso de “afino del acero”, por el cual el arrabio (hierro de primera fundición con alto porcentaje de carbono) se transforma en acero, eliminando impurezas (como azufre o silicio) y el exceso de carbono.
Desarrollo
Como materiales de partida para la fabricación de los ladrillos se utilizó magnesia electrofundida (de diferente pureza y distribución granulométrica), grafito (pureza ≥ 95% en peso) y antioxidantes: aluminio metálico (Al) y silicio (Si). Como ligantes se adicionaron resinas fenólicas Novolac y Resol. Los tres ladrillos, identificados como A, B y C, fueron formulados con el mismo contenido de magnesia (85,0 % en peso), grafito (8,2 % en peso), antioxidantes (4,0 % en peso) y ligante (2,8 % en peso).
La pureza de la magnesia se determinó mediante fluorescencia de rayos X (FRX) utilizando un espectrómetro PANanalytical Axios mAX. Mientras que la distribución de tamaño de partículas (DTP) del MgO se obtuvo por tamizado. La granulometría se clasificó, de forma cualitativa, como agregados de MgO “grandes” (tamices ASTM: 4, 5, 6, 7, 8 y 10) y “medios” (tamices ASTM: 7, 8, 10, 12, 16, 20 y 140).
Siguiendo un procedimiento similar al utilizado en la fabricación de productos refractarios comerciales, se conformaron ladrillos, por prensado uniaxial, de dimensiones: 229x152x76 mm3 bajo una presión de 135 MPa (R. A. Landy, 2004). Para los ensayos físicos (densidad y porosidad) y observación microestructural, se obtuvieron muestras de los tres ladrillos en estado de preparación (EP) por medio de cortes con una sierra diamantada.
La porosidad aparente (πA) y la densidad aparente (ρA) se midieron mediante el método de Arquímedes utilizando querosene como líquido de inmersión. La densidad verdadera (ρV) se determinó utilizando el método por picnometría, a partir de medidas de peso utilizando querosene como fluido, empleando un recipiente de volumen calibrado (picnómetro). El ensayo se realizó por duplicado sobre 20 g de muestra, obtenida a partir de la trituración y molienda, y tamizado (pasante malla ASTM N°70). La porosidad verdadera (πV) y la porosidad cerrada (πC) se calcularon utilizando las ecuaciones (1) y (2):
Para el examen microestructural, muestras de los tres ladrillos en estado de preparación (EP) se embutieron en resina. Las mismas fueron sometidas a un proceso de desbaste con papeles de SiC desde granulometría #100 hasta grano #1200 y luego fueron pulidas, sucesivamente, con pasta de diamante de 6, 3 y 1 μm. Se utilizó un microscopio Carl Zeiss Axiotech (con un analizador de imágenes KS300) para las observaciones de microscopía óptica (MO). La microestructura también se observó mediante microscopía electrónica de barrido (MEB) utilizando un microscopio FEI Quanta 200 con análisis de energía dispersiva (EDS).
El análisis microestructural se completó con la identificación de las fases cristalinas, aplicando la técnica de difracción de rayos X (DRX), utilizando un difractómetro Philips X'Pert con radiación CuKα (40 kV, 30 mA). Los difractogramas se obtuvieron en el intervalo angular 2θ entre 10-80°, con un paso de 0,02° (1 s por paso). La interpretación de los mismos se realizó con el software PANalytical - HighScore.
La resistencia al ataque químico se estudió mediante un ensayo de corrosión estática (denominado “cup test”). Para esto, se confeccionaron crisoles de las siguientes dimensiones: base = 70 x 70 mm2 y altura = 70 mm, con un orificio central de 30 mm de diámetro y 40 mm de profundidad. En cada orificio se colocó 35 g de escoria de convertidor LD. El ensayo de “cup test” se llevó a cabo a 1600°C durante 2 horas en atmósfera de aire. Luego del mismo, los crisoles se cortaron a la mitad (longitudinalmente) y se embutieron en resina. El proceso de desbaste y pulido de las caras, expuestas tras el corte, fue similar al realizado para las muestras de los ladrillos EP (descripto arriba).
Mediante imágenes de microscopía óptica se cuantificó la intensidad del ataque de la escoria sobre cada ladrillo midiendo el área de penetración (AP) en el fondo del orificio central del crisol.
El tamaño de grano cristalinos de magnesia electrofundida se determinó aplicando un método de medición lineal (L. M. Akselrod et al, 2014) utilizando imágenes obtenidas de microscopía óptica y un software de procesamiento de imágenes (JMicronVision). Dada la morfología no equiaxial de los granos, se midieron la altura (línea vertical) y el ancho (línea horizontal) máximo de cada grano, figura 1. Usando la ecuación (3) se determinó el tamaño de grano promedio.
En la ecuación (3), Scp es el tamaño medio de grano (en μm), S es la suma de los tamaños de grano (en μm) y n es el número de granos examinados.
Resultados
En la Tabla 1 se muestran los contenidos de los principales óxidos presentes en los agregados de magnesia y la composición química de la escoria de contenedor LD utilizada en el ensayo de corrosión.
La figura 2 muestra la distribución granulométrica del MgO empleado en cada uno de los ladrillos, donde se observa la disposición de los agregados de magnesia electrofundida en los intervalos de granos denominados “grandes” (centrado en 3,5 mm) y “medios” (centrado en 1,5 mm).
Los valores de las porosidades y las densidades (aparente y verdadera) de los ladrillos se presentan en la Tabla 2.
Antes del ensayo de corrosión, se observó la microestructura de los ladrillos mediante microscopía de luz reflejada. La figura 3 muestra, mediante microscopía de luz reflejada (aumento x50), imágenes de los ladrillos preparados
A partir de las imágenes obtenidas por microscopía óptica de los ladrillos, se determinó el tamaño promedio de grano (las mediciones se realizaron sobre 275 granos). Estos valores, junto con los valores máximos y mínimos obtenidos en las mediciones de cada ladrillo, se presentan en la Tabla 3.
El análisis de EDS se utilizó para medir la relación CaO/SiO2 (C/S) en puntos triples y límites de grano de los agregados de MgO. La relación C/S se presentan en la Tabla 3 (valor promedio obtenido de 10 mediciones).
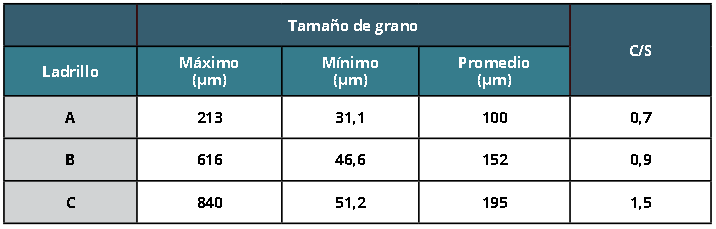
Tabla 3: Valores de los tamaños de granos en agregados de magnesia electrofundida y de la relación CaO/SiO2 entre bordes de grano de MgO.
En la figura 4 se muestran los patrones de DRX de cada una de las muestras en estado de recepción. Estos difractogramas confirman la presencia de silicio (Si) aluminio (Al), grafito (C) y magnesia (MgO), como los componentes principales de todas las muestras, en concordancia con el análisis microestructural con MO, MEB y EDS.
Las microestructuras que se presentan en las figuras 5, 6, 7 y 8, fueron obtenidas por microscopía electrónica de barrido luego del ensayo de corrosión estática. En estas micrografías se puede observar que los ladrillos de MgO-C en contacto con la escoria de convertidor muestran diferentes zonas y grados de reacción.
En la figura 5 (a-c) se distinguen cuatro zonas en la interfaz refractario/escoria: (i) una zona con escoria sin reaccionar, (ii) una zona de reacción (con cambios en el contenido de fase en comparación con el refractario original), (iii) una zona intermedia o de transición (con cierta penetración y reacción con la escoria) y (iv) una zona del refractario sin reaccionar.
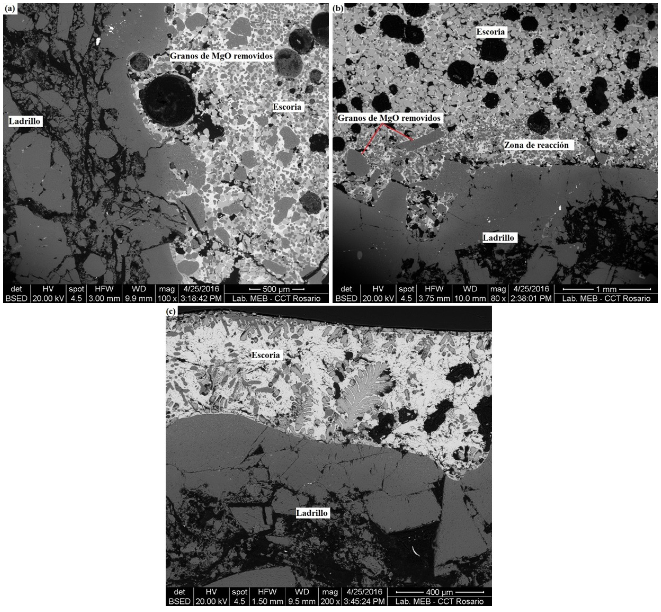
Fig. 5: Imágenes de MEB de la interfaz escoria/refractario correspondiente al (a) ladrillo A, (b) ladrillo B y (c) ladrillo C.
Las figuras 6, 7 y 8 muestran con mayor detalle la zona de reacción refractario-escoria de los ladrillos A, B y C, respectivamente. Un análisis de EDS de las distintas fases presentes se muestran en la Tabla 4, 5 y 6.
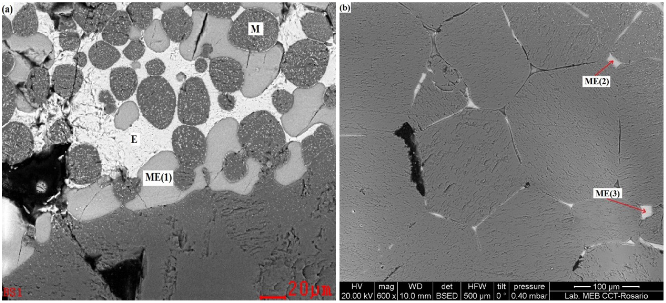
Fig. 6: Micrografía del ladrillo A corroído después del contacto con escoria de LD. (a) interfaz refractario-escoria y (b) ataque de escoria intergranular.
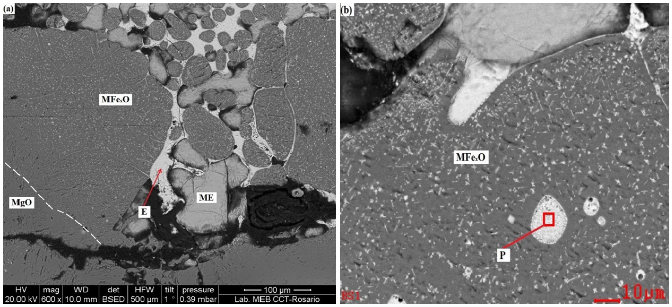
Fig. 7: Micrografía MEB del ladrillo B que muestran (a) la zona de reacción escoria/refractario y (b) grano de MgO que contiene Fe2O3 y poro con escoria.
Las determinaciones del área de penetración (AP) de la escoria, medida en cada ladrillo tras el ensayo de corrosión a 1600°C, presentaron los siguiente s valores: AP (ladrillo A) = 6,9 mm2, AP (ladrillo B) = 6,6 mm2 y AP (ladrillo C) = 5,0 mm2.
Discusión
Según la composición química de los agregados de magnesia (Tabla 1), el ladrillo C presenta un grado de pureza ligeramente superior. La resistencia a la corrosión de los refractarios MgO-C será mayor cuando los agregados de magnesia presenten una mayor concentración de MgO (menor contenido de impurezas). Las impurezas presentes en la magnesia no existen como óxidos independientes, sino que se combinan entre sí o con el MgO formando compuestos que se ubican en los puntos triple y en los bordes de grano de MgO. Las impurezas (FexOy, SiO2, CaO, Al2O3, Cr2O3) forman segundas fases, como los silicatos, responsables de la unión entre los granos a temperaturas más bajas (R. A. Landy, 2004). Estas fases presentan temperaturas de fusión más bajas que la magnesia. En aplicaciones metalúrgicas a altas temperaturas, el ablandamiento de las uniones en los bordes de grano conduce a la pérdida de la integridad del agregado de MgO y proporciona caminos críticos para el ataque de la escoria.
Por su lado, las escorias de acería presentan una diversidad de óxidos, conteniendo principalmente CaO, Al2O3, SiO2, FeO/Fe2O3 y MgO. Los porcentajes de estos óxidos varían de acuerdo con la etapa del proceso de acería en el cual la escoria es utilizada. En el caso de la escoria seleccionada, utilizada en la industria del acero (típica de un convertidor LD), presenta un considerable contenido de óxido de hierro (del orden del 33 % en peso), lo que la hace una escoria con un importante grado de agresividad a la temperatura de operación (1600-1650°C) (E. Benavidez et al, 2014).
La densidad real medida es la misma, para todas las muestras, debido a la similitud de las materias primas utilizadas en la fabricación de ladrillos. Por otro lado, los ladrillos B y C presentan menor porosidad aparente (abierta). Según los valores determinados de la porosidad verdadera (πV) y de la porosidad aparente (πA), se obtienen los valores de porosidad cerrada (πC) de 2,3 % vol. (ladrillo A), 3,9 % vol. (ladrillo B) y 2,6 % vol. (ladrillo C). Si consideramos que uno de los mecanismos de la corrosión química de los ladrillos refractarios comienza con la penetración de la escoria a través de los poros abiertos, entonces, la porosidad abierta es la que impactará más directamente en la resistencia a la corrosión. Teniendo entonces en cuenta, principalmente, los valores de la porosidad abierta se espera que los ladrillos B y C presenten una mayor resistencia al ataque de la escoria.
De acuerdo con la distribución granulométrica de los agregados grandes, figura 2 (a), no se aprecia una diferencia significativa en tamaño entre 2 y 5 mm para los tres ladrillos. En cuanto a los agregados de tamaño medio, figura 2 (b), los ladrillos A y B (barras rojas y negras) muestran un mayor porcentaje de partículas con dimensiones superiores a 1 mm, mientras que el ladrillo C (barra azul) exhibe un porcentaje más elevado en partículas con tamaños que oscilan entre 100 µm y 1 mm. Esto conduce a concluir que el ladrillo C posee una DTP de granos de MgO más finos. Sumado a esto se debe considerar que el tamaño de grano dentro de los agregados de MgO (Tabla 3) es considerablemente mayor en el ladrillo C (casi el doble, en promedio, que el ladrillo A). Un tamaño de grano policristalino más grande en los agregados de magnesia significa una menor superficie de los límites bordes de los granos, los cuáles que contienen fases secundarias que pueden ser penetradas por la escoria líquida. Por lo tanto, un tamaño de grano más grande disminuye el área de contacto expuesta a la reacción refractario/escoria, al limitar el área de la superficie de contacto, y así mejora la resistencia a la corrosión (E. Benavidez et al, 2014) (W. E. Lee et al, 1999). Por otro lado, resulta relevante considerar la relación C/S en bordes de grano de MgO, ya que determina la naturaleza de las fases que se pueden formar. Es importante tener la relación C/S > 2 para obtener fases más refractarias como silicatos dicálcicos y tricálcicos en los agregados (S. R. Bragança, 2012). Como se mencionó anteriormente, el promedio de la relación C/S medida en las áreas de bordes de grano y puntos triple indica la presencia de fases secundarias amorfas que generan caminos críticos que pueden ser penetrados por la escoria líquida. Los valores de Tabla 3 indican una mayor relación C/S en los granos de MgO usados en la fabricación del ladrillo C. Así, teniendo en cuenta el análisis realizado sobre los valores obtenidos de DTP, tamaño de grano y relación C/S, se espera que el ladrillo C experimente una mayor resistencia a la penetración de la escoria.
En la figura 3 se muestra que los granos de magnesia electrofundidos (MF) están presentes como agregados (partículas > 200 µm) y en la matriz (partículas < 200 µm). Además, en la matriz se observa la presencia de hojuelas de grafito (G) y aluminio metálico (A) como partículas brillantes. Según el análisis EDS, estas partículas brillantes corresponden a la presencia de aluminio (Al) utilizado como antioxidante. Por otro lado, el análisis EDS confirma la presencia de Si como otro tipo de antioxidante añadido a los ladrillos.
Los difractogramas de DRX, figura 4, muestran picos similares para los tres ladrillos y confirman que el grafito (C) y la magnesia (MgO) son los componentes principales, mientras que el silicio (Si) y el aluminio (Al) están presentes como fases secundarias. La obtención de similares difractogramas de DRX en los tres ladrillos, es consistente con el uso de materias primas y porcentajes similares empleados en la conformación de los mismos.
La escoria del convertidor utilizada en el ensayo de corrosión estática tiene una basicidad binaria CaO/SiO2 = 4,2 y un contenido significativo de óxido de hierro ≈ 33% en peso. Un alto contenido de óxido de hierro (FeO/Fe2O3) presente en la escoria reduce significativamente la temperatura de fusión de los productos de reacción escoria/refractario (R. A. Landy, 2004). Por otro lado, la saturación de escoria con MgO tiene una influencia crítica en el proceso de disolución del refractario en la escoria (Zhang et al, 2000). La velocidad de corrosión disminuye con el incremento de MgO en la escoria. Con un 8% de MgO en la escoria de LD utilizada, se asume que la escoria está saturada a 1600°C (Jansson et al, 2004).
En la zona de la escoria, figura 5 (a-c), se pueden observar granos de MgO que han sido removidos del ladrillo. Estos granos de MgO, pertenecientes al ladrillo original, son fácilmente identificables debido a su apariencia distintiva en contraste con la escoria circundante.
Por otro lado, la figura 6 muestra con mayor detalle el ataque de la escoria sobre el ladrillo A y las fases que se generaron por la corrosión. Se identifican los granos electrofundidos de MgO que fueron desagregados y arrastrados hacia la escoria. Estos granos, identificados como M, son ricos en MgO (( 88%), Fe2O3 (( 8%) y CaO (( 2%), conteniendo en su interior magnesio-wustita (MgO-FeO) o magnesio-ferrita (MgO-Fe2O3). La disolución de la magnesia por los óxidos de hierro y la formación de una solución sólida de magnesio-wustita provoca un cambio perjudicial de volumen (J. Poirier et al, 2007). Según los diagramas de equilibrio binario MgO-FeO y MgO-Fe2O3, a 1600°C el MgO puede disolver hasta ≈ 70% FeO o ≈ 100% Fe2O3 sin presencia de fase líquida. Por lo tanto, se considera que la penetración de la escoria (con ≈ 33% en peso de óxido de hierro) a través de los granos de MgO puede desarrollarse mediante difusión en estado sólido. En este caso, las especies Fe+2/Fe+3 difunden desde la escoria hacia los granos sólidos de MgO. En la figura 7 (a) y 8, se puede distinguir una capa de magnesio-wustita o magnesio-ferrita (MFexO) en la región del ladrillo cercana a la interfaz de reacción escoria-refractario.
En la zona de reacción refractario/escoria de los tres ladrillos, figuras 6, 7 y 8, se observan granos de color gris claro (etiquetados como ME) que contienen CaO (( 51,5 ±1,6%), SiO2 (( 31,9 ±1,5%) y MgO (( 9,5 ±3,1%), que son asociados con la fase sólida merwinita (3CaO.MgO.2SiO2) con una composición química estequiométrica igual a 51,2% CaO, 36,6 % SiO2 y 12,3 % MgO. Esta fase promueve la formación de líquido a la temperatura del ensayo de corrosión ya que presenta una temperatura de fusión de 1575 °C.
La fase continua, marcada como E, tiene un alto contenido de CaO (≈ 40 ±2 %) y Fe2O3 (≈ 35 ±2 %) con menores porcentajes (en peso) de SiO2 (6-8 %), MgO (7-10 %), Al2O3 (3-7 %) y MnO (4-6 %). La misma corresponde a una composición aproximada de la escoria original (Tabla1). De acuerdo con este análisis, no se observa un grado de disolución de la magnesia en la escoria, lo que da indicios de que la escoria está saturada a 1600°C.
Esta fase E se considera líquida a la temperatura del ensayo (1600°C) y cuando entra en contacto con agregados de MgO avanza a través de las uniones de los granos donde reacciona con las fases de las impurezas inicialmente ubicadas en los bordes de los granos. En un estado más avanzado de la reacción, las uniones intergranulares se rompen y los granos de magnesia se desprenden del agregado. Las micrografías de MEB, junto con el análisis EDS, dan muestra de que los agregados electrofundidos de MgO han sido penetrados por vía intergranular por especies del tipo Fe3+/Fe2+, Mn2+ y Ca2+.
De las observaciones realizadas sobre la microestructura de las tres muestras se puede inferir, cualitativamente, que el mayor grado de corrosión se observó en el ladrillo A. Esta observación es confirmada cuantitativamente por las determinaciones del área de penetración de la escoria, por la cual: AP (ladrillo A) > AP (ladrillo B) > AP (ladrillo C).
Conclusiones
A partir de la microestructura analizada después del ensayo de corrosión estática a 1600°C de tres ladrillos de MgO-C que contienen diferentes calidades de MgO electrofundidida, se llegan a las siguientes conclusiones.
El área más pequeña corroída por la escoria se observa en el ladrillo C. Esto se atribuye a la mayor pureza de la magnesia electrofundida, la baja porosidad abierta y la menor porosidad total, la mayor relación CaO/SiO2 en los límites de los granos y el mayor tamaño de grano dentro de los agregados de magnesia.
De acuerdo con las observaciones realizadas a lo largo del perfil de corrosión, se establece que los mecanismos de ataque de la escoria son: (i) la penetración de los granos de MgO por el óxido de Fe/Mg para formar una solución sólida de magnesio-wustita y/o ferrita de magnesio, (ii) la infiltración de la escoria a través de los poros abiertos y (iii) la reacción de la escoria con las fases silicato, ubicadas en los bordes de los granos dentro de los agregados de MgO, generando compuestos de bajo punto de fusión, la destrucción de las uniones entre granos y, finalmente, el desagregado de los granos de MgO. Este último mecanismo parece ser el de mayor incidencia en el ataque químico realizado por parte de la escoria utilizada.